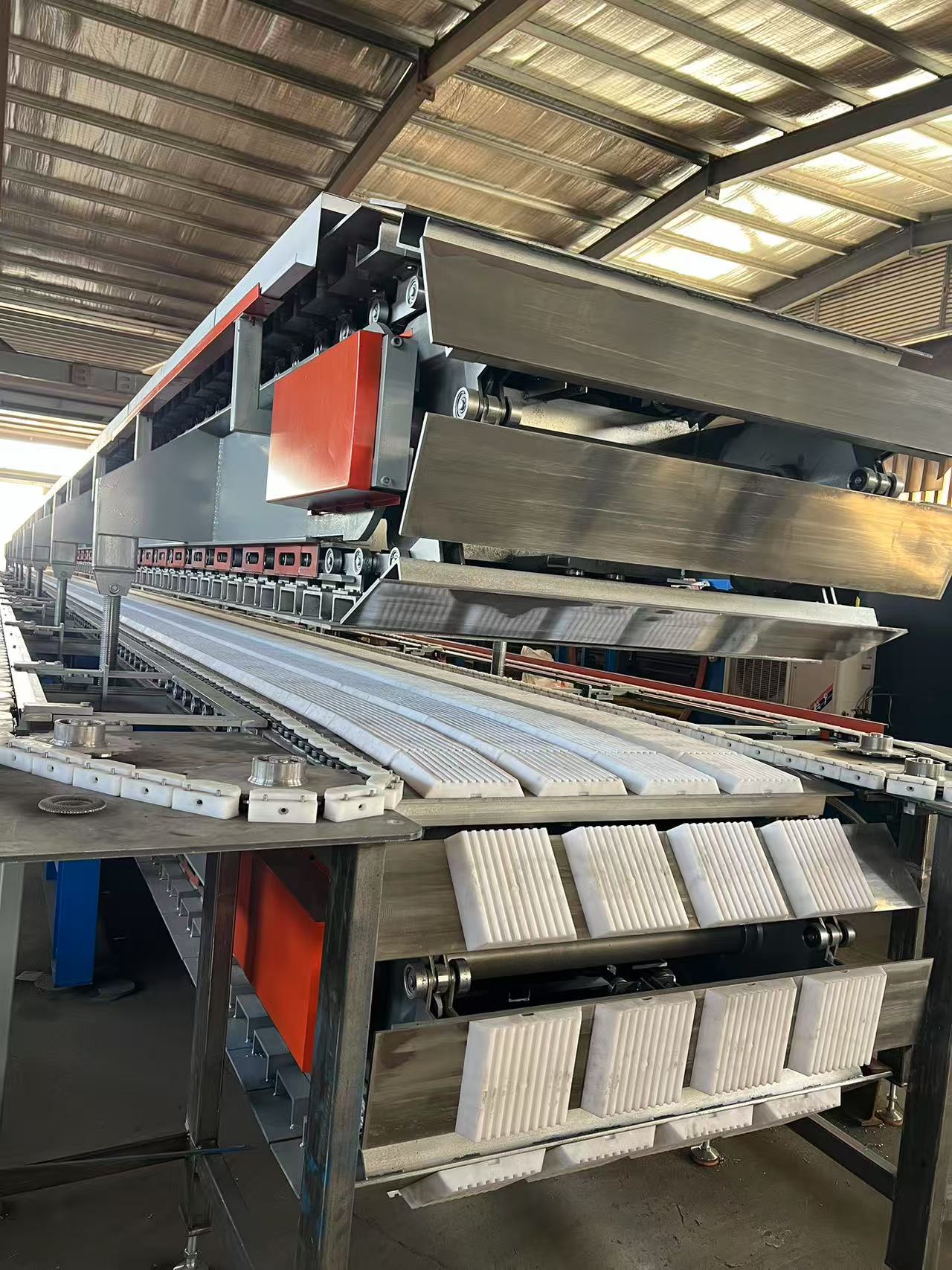
Wuxi Zhongshuo International Trading Co., ltd, a professional designer, manufacturer and trader of Sandwich Board Production Line and Exterior wall insulation equipment. It is the enterprise with the largest scale and strongest competitiveness in the domestic industry of this kind, and its manufacturing facility is located in Langfang, Hebei province.
1. Un-coiling system
Function
The uncoiler adopts hydraulic cantilever tightening type, which is mainly used for steel coil feeding and recycling. The lifting trolley carries the coiling material to the unwinding machine, and the loading and unloading of the coiling material is realized through the lifting mechanism.
The core shaft of the uncoiling machine tightenes the coiling material in the form of inclined plane movement, and the center of the coiling material is adjusted by the hydraulic cylinder. The inner support plate on the core shaft can be installed with different specifications of the backing plate to ensure the requirements of different inner diameters of the coiling material. The core shaft of the uncoiling frame is driven by the motor to realize the plate active opening, and can also be used for the recovery of unprocessed plates.
2. Forming machine system
Function
The guide device at the front end of the forming machine adjusts the steel plate to the line reference; The forming machine roller presses the plate forming (Great Wall plate, wall panel, cold storage plate), and sends the mold plate to the interface raceway connecting the forming machine and the preheating furnace.
Composition
The forming machine system consists of an upper forming machine, a lower forming machine, a pressing machine platform placed on the upper pressing machine, and an upper and lower interface raceway connecting the forming machine to the preheating furnace.
3. Foaming machine system
polyurethane glue spraying machine technical program:
Polyurethane foaming machine is a small flow of two component glue mixing device, widely used in polyurethane continuous production line equipment.
4. Hot air circulation device
The dual-track temperature control system uses hot air circulation for heating. After the circulating air is heated by the heating device, it is sent to the heating duct by the fan for heating the upper and lower track panel of uniform speed. Through the track panel, the composite plate is heated to make the polyurethane foam foaming and curing more stable, and the foam and the plate surface are more firmly bonded, reducing the foam spots and bubbles to a certain extent.
The equipment adopts electric heating, the heating form is hot air heating, the heat exchange device is placed above the double track, and the double belt chain plate traveling at uniform speed is heated by separate heating air ducts on the upper and lower floors. Considering the safety of cyclopentane foaming, explosion-proof fans should be used for heating circulation fans.
5. Double track system: 24M
The double track laminate machine is installed in the middle of the continuous production line, which is used for the sandwich plate to mature and form under a certain pressure. The role of the upper and lower track is mainly to overcome the foaming force generated by polyurethane foam, and the double track is used as an active template for continuous production, which needs to avoid plate deformity and surface scratching to ensure the production of high-quality composite boards
Composition
The double track is mainly composed of upper and lower track, left and right side belt, transmission mechanism and screw lifting system.
6. Band saw automatic tracking cutting system
Function
The main function of the band saw machine is to automatically measure the length parameters of the board according to the needs of the length encoder, and automatically cut the continuous finished board without stopping the production line. It also absorbs the dust generated during cutting.
7. Large-span sucker palletizing system
Composition
The sucker palletizer consists of a fast roller table, a front and back turning device, a sucker part, a driving part, a gantry frame, and a conveying roller table after stacking.
Function
The fast roller table makes the composite plate cut by the band saw quickly separate from the plate before cutting; And transport the plate to the designated location; The turning device turns an odd number of corrugated plates 180° to facilitate the stacking of plates; The sucker parts are stacked according to the type of plates, and the plates after stacking are neat and beautiful; After stacking, the conveying roller delivers the sheet.
The front roller table is equipped with a light-controlled positioning mechanism. When the length of the stacking board is less than 7.5 meters, two pieces can be stacked together.
Greater than 7.5 meters, only one stack.
8. Packaging system
Function
After the stacking plate is transported to the baler by the roller table, the plate is packed from beginning to end with a film. During the packaging, the number of strengthening packaging rings of the head and end is manually controlled. The overlap amount of the film winding can be adjusted within the range of 0 ~ 200mm. The conveying roller delivers the finished sheet metal.
Main structure
The packing system is mainly composed of a baler, an outlet roller table, etc. The outlet roller table has a space for forklift to lift the workpiece.